

Catalytic performance was evaluated through parametric studies.
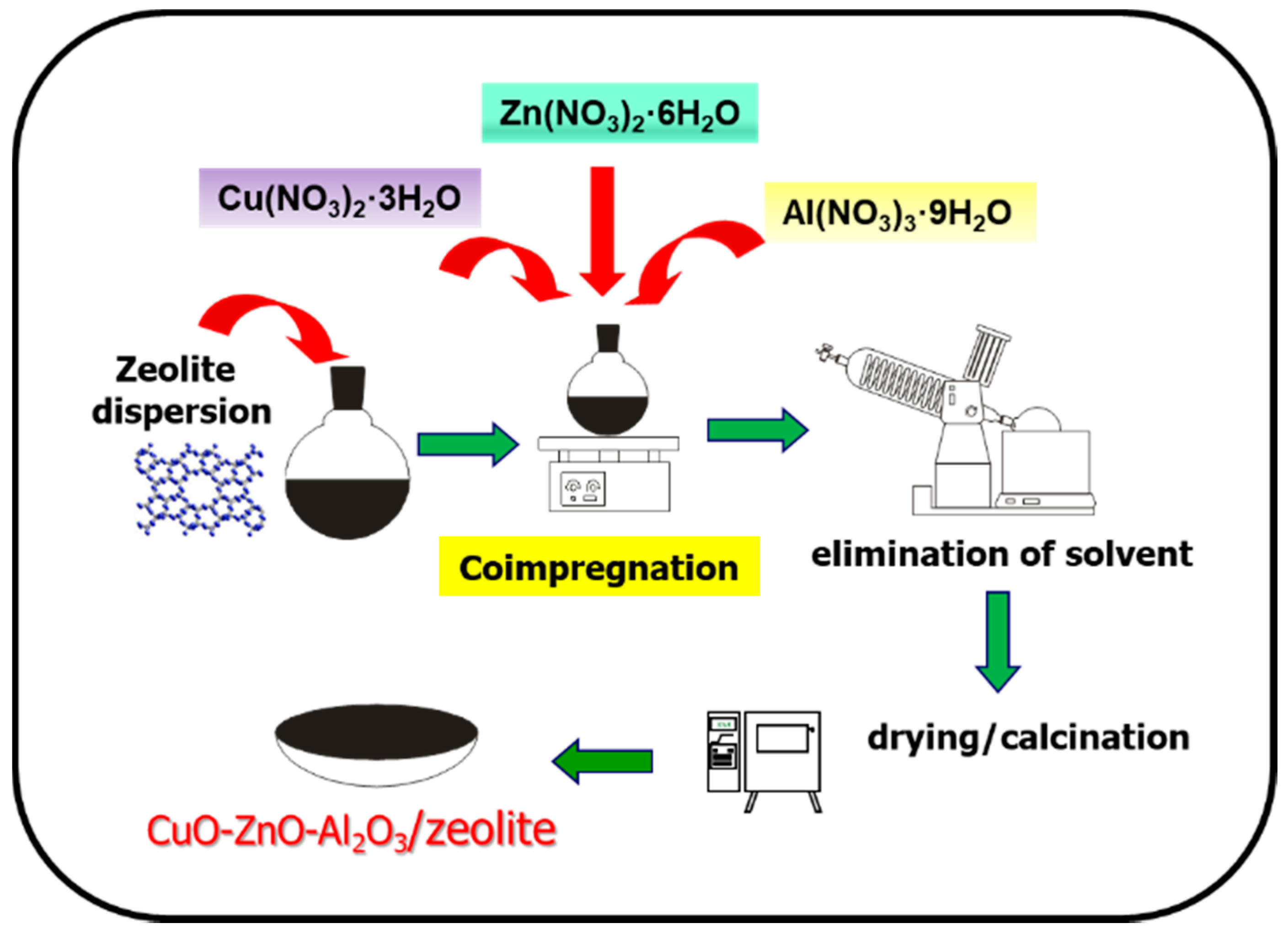
The PdZnAl catalyst was shown to be far superior to a conventional copper-based methanol catalyst when operated at relatively high temperatures (i.e., more » >300☌), which is necessary for MTG-type applications. For this application, a Pd/ZnO/Al2O3 (PdZnAl) catalyst previously developed for methanol steam reforming was evaluated. In this study, we investigated direct conversion of syngas to distillates using methanol and dimethyl ether intermediates. To accomplish this, modifications to the traditional methanol-to-gasoline (MTG) process were investigated.
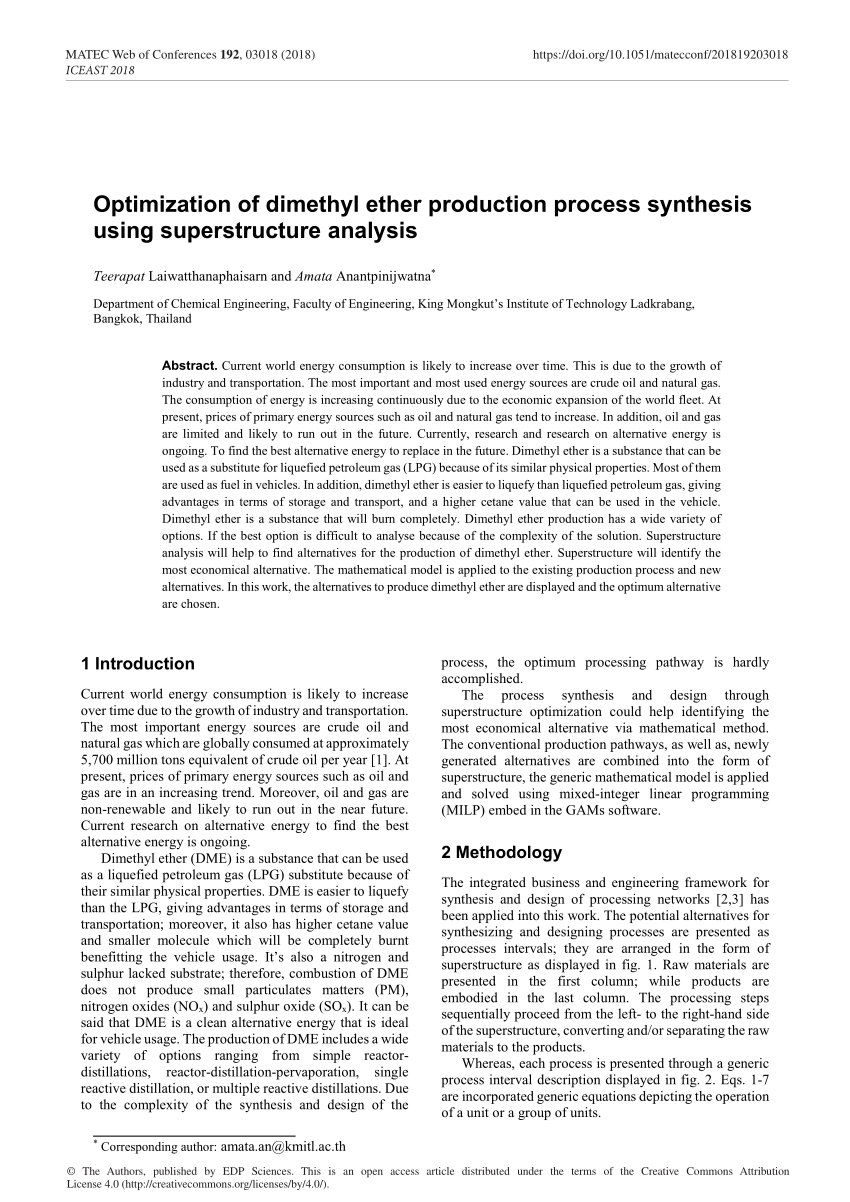
The objective of the work was to enhance price-competitive, synthesis gas (syngas)-based production of transportation fuels that are directly compatible with the existing vehicle fleet (i.e., vehicles fueled by gasoline, diesel, jet fuel, etc.). Additionally, CO2 formation was problematic as PdZn was found to be active for the water-gas-shift (WGS) reaction, under all the conditions evaluated. Hence, two types of sites are required for the direct conversion of syngas to DME: 1) PdZn particles are active for the synthesis of methanol from syngas, and 2) acid sites which are active for the conversion of methanol to DME. A correlation between DME selectivity and the concentration of acid sites of the catalysts has been established. Results indicate that PdZn particles are more active than Pdº particles for the synthesis of methanol and less active for CH4 formation. A catalyst with 5% Pd and a Pd:Zn molar ratio of 0.25:1 has been identified as the preferred catalyst. By studying the effect of the Pd loading and the Pd:Zn molar ratio the formulation of the Pd/ZnO/Al2O3 catalyst was optimized. Undesirable CH4 formation was observed, however, can be minimized through choice of process conditions and by catalyst design. Increased GHSV’s and H2/CO syngas feed ratios also enhanced DME selectivity. Selectivity to DME increased with decreasing operating temperature, and increasing operating pressure. The Pd/ZnO/Al2O3 catalyst was more » thus further investigated for methanol and DME synthesis at P=34-69 bars, T= 250-380☌, GHSV= 5 000-18 000 h-1, and molar feeds H2/CO= 1, 2, and 3. On the contrary, a Pd/ZnO/Al2O3 catalyst was found to be highly stable for methanol and DME synthesis at 380☌. A commercial Cu/ZnO/Al2O3 catalyst, utilized industrially for the synthesis of methanol at 220-280☌, suffers from a rapid deactivation when the reaction is conducted at high temperature (>320☌).

380☌) are necessary when combining methanol and DME synthesis with a methanol to gasoline (MTG) process in a single reactor bed. Studied were temperatures of operation ranging from 250☌ to 380☌. « lessĪ Pd/ZnO/Al2O3 catalyst was developed for the synthesis of methanol and dimethyl ether (DME) from syngas.
